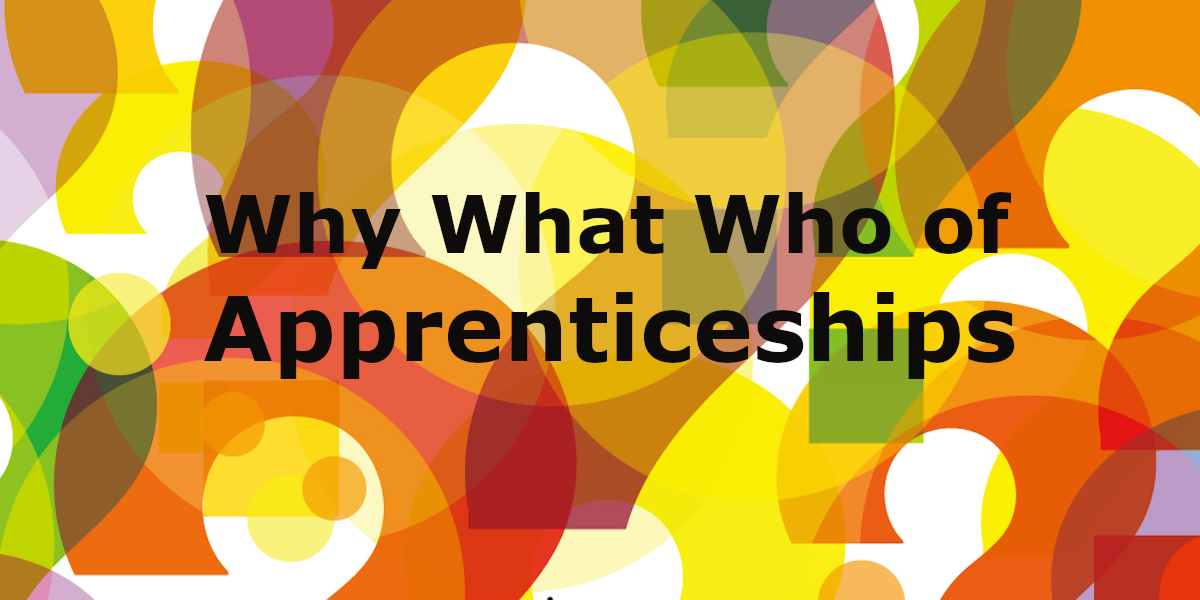
Why, What, Who of Apprenticeships
This week we take a brief dive into why businesses take on apprentices, what businesses apprenticeships suit and who we generally work with. We also hear from Regan, who has just completed his apprenticeship and Sam who is 1 month in.
As we move into Autumn, change is upon us both in terms of the season and the economic outlook of the UK. The furlough scheme is winding down, the result of which may mean a sharp rise in unemployment and a high number of young people looking for their next opportunity to get into work or training.
The government has launched several schemes in an attempt to increase opportunities for young people and we wait to see what effect Kickstart and the revival of Traineeships has on the people facing unemployment. We are very much focused on apprenticeships and the government has introduced incentives in an attempt to encourage businesses to offer new opportunities.
Why take on an apprentice?
For many businesses, skills gaps have been a barrier to growth and a big driver to take on apprentices. Creating their own pipeline of new recruits that can be trained specific to the skills and capabilities the organisation requires has helped to ensure they have an effective workforce. Apprenticeships produce an employee who has learnt the ways of the business whilst consistently upskilling over several years, so the business gets the staff member they need at the end of the process.
Retention rates of apprentices after they have completed their training also tend to be high giving them a workforce that is able to grow with the business. Neill Brodey of Norbar Toque Tools recently commented that one of their apprentices has now been with the firm for 54 years. Similarly, Beverly O’Farrell of FMB Oxford commented that their apprenticeship programme has been running for over 10 years training countless apprentices and only one has left the business (after 10 years of employment).
What businesses does an apprentice suit?
The employment of an apprentice or the use of an apprenticeship for an existing employee suits a business looking to make a long term investment in their workforce. They are not a quick fix taking between 18 and 42 months to complete depending on the level and require the employee to be given time out of their working hours to train. Many businesses have an annual rolling recruitment of apprentices which, over time, gives them a consistent annual pipeline of skilled people to fully deploy across the organisation.
Who do ETT generally work with?
We are specialists within the engineering, manufacturing and maintenance sector. As a rule of thumb, the businesses we work with all produce something or maintain mechanical/electrical equipment. We work with both levy and non-levy businesses who trust us to deliver high quality apprenticeships to their employees.
Hear from our apprentices
Below are two examples from apprentices we work with, their thoughts on their apprenticeship programme and their experience of ETT.
Regan – Apprentice Engineer at Chiltern railways – Apprenticeship Complete July 2020.
I have spent the last 4 years learning to maintain the fleet of trains. The work is enjoyable and varies day to day which I find exciting and keeps me intrigued.
During my apprenticeship I have not only completed a level 3 NVQ in mechanical engineering but have also progressed at college with an HNC and extended it then to a HND in mechanical engineering which should put me in a good position for future progression.
I would like to look at moving from working on the shop floor to becoming a technician in the near future and hopefully progress from there onwards.
During the apprenticeship there was always going to be great times and some low times. Engineering Trust Training has really helped me over the 4 years and I really appreciated having Mark (ETT Training Officer) there as an external person to talk to and discuss ways I could improve. He not only assessed my work but also gave me advice on various situations throughout the journey. We built a great relationship and I believe he provided me with great training and help motivate me to get the best quality work possible.
I would definitely recommend doing an apprenticeship to anyone as it pushes you as a person to try achieve your goals. It also develops a good understanding of the work environment which puts you in a good position to progress quickly once your training is complete. I would equally encourage businesses to take on apprentices in order to get great, well trained people into your company.
Sam – Apprentice Engineer at FMB Oxford – 1 month into the Apprenticeship
I knew that I wanted to do engineering after I did my work experience at Algar Electric Motors LTD. I really enjoyed it there and it was very hands on and applied for my current role after I saw met Engineering Trust Training at an apprenticeship event at Witney college.
I decided to do an apprenticeship rather than A-levels because I like being hands on when learning rather than doing theory based stuff at school which I might never need. Also I am getting paid to learn rather than building up student debt so that was really appealing.
I found my apprenticeship by applying online on the ETT website. I had to upload my CV and my predicted grades and do some online assessments which tested my maths, English and other skills. I then had a phone interview with one of the ETT Training Officers where they asked me questions to find out what discipline of engineering I was interested in. I was shortlisted for the role at FMB Oxford where I had one zoom interview and one face to face. When I went in for my face to face interview I got a factory tour and saw all the high tech components and machines they were making, I found it intriguing!
FMB was an ideal role for me as it is local and easy to get to. It is also a really interesting business where not every product is the same, they are manufactured to each customer’s specification so the work is really varied. I’m doing an Engineering Technician apprenticeship where I will be doing a mixture of mechanical and electrical engineering, learning about beamlines and all the many different components we make here.
In my first month I’ve been shadowing some of the more experienced techs, helping them with jobs in some of the smaller components like cryocooler boxes and linear slides. I start at college soon so will be spending less time in company whilst I complete my Foundation Competencies.
I am really excited to learn more about what we do at FMB and developing my own personal skills. I would advise anyone looking to do an apprenticeship to think about what they want to do in the future and find something they are going to enjoy.
Beverly O’Farrell of FMB Oxford – ‘Sam has just started with us and he already seems to be a great choice and addition to the team here!’
Image Credit free background photos from pngtree.com